EHS (Environmental Health and Safety) Global Policy
For ONO group, to realize a sustainable society and continuous growth, it is important to conduct business activities that address EHS (environment, hygiene/health, safety). Therefore, we established EHS global policy.
EHS (Environmental Health and Safety) Promotion System*
At the EHS Committee consisting with members of production sites, research institutes, headquarters, and other major sites, we share information on amendments to the law, improve risk assessment skill, and share the best practices on the corrective action of occupational injuries. The EHS Committee works with the safety and health committee of each site. In addition, the Sustainability Promotion Department implements internal audits (EHS self-checks), reports the results at the EHS Committee, and implements management review. In this way, management members are involved in EHS management.
- The Organization names are as of April 1, 2024.
Building the EHS Management System
We set targets for sustainability, including environmental and occupational safety and health and promote building the EHS (Environmental Health and Safety) management system with the aim of achieving these targets.
The EHS Management System that we are building is stipulated by the departments involved in EHS promotion of headquarters concerning entire company requirements related to EHS as the SOP (standard operating procedure). In addition, based on the SOP, operations of the SOP are stipulated for each department. Thereby, concrete actions for the achievement of entire company targets that have been established are stipulated at the same level throughout the company. Based on ISO45001 (Occupational Safety and Health Management System) and ISO14001 (Environmental Management System), the SOP stipulates compliance with laws and regulations related to occupational safety and health, the environment, and fire-prevention and disaster-prevention, etc. and technical requirements that are not provided for by laws and regulations but require actions to be taken. In addition, by stipulating and implementing internal audits, it plans to implement PDCA to promote continuous improvement. In addition, it stipulates management review so that management members are involved.
We started to build the EHS Management System in FY2021 and aim to create an SOP for 97 items by FY2024 in order to establish the EHS Management System. We have completed an SOP for 53 items by FY2023.
In addition, along with the creation of an SOP, we started internal audits for compliance with laws and regulations in FY2021 and management review in FY2022.
We will continue to promote the building of the EHS Management System, protect occupational health and safety, and maintain and improve the environment in our operation areas so that we can be a company that can obtain trust from stakeholders as well, including the community and employees.
EHS Management system flamework
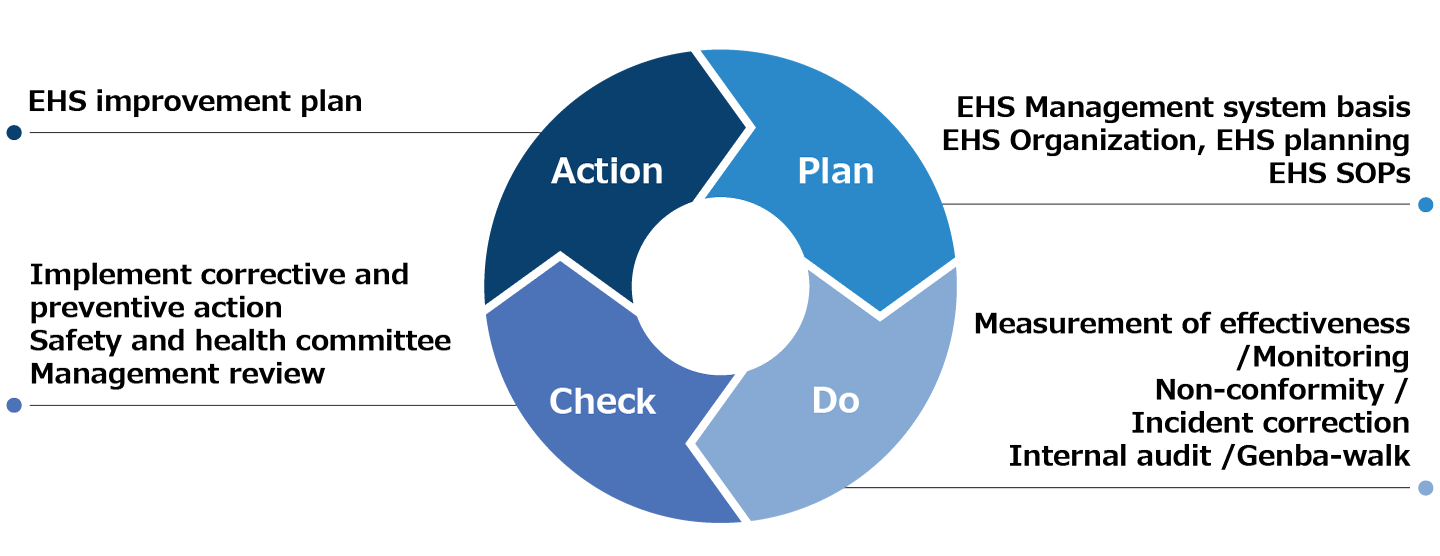
Production site name | |
---|---|
Fujiyama Plant | Certified |
Yamaguchi Plant | Certified |
Scope of ISO 14001 certification at production sites | 100% |
- The Joto Plant of TOYO Pharmaceutical Co., Ltd., one of our group companies, has also acquired ISO14001 certification.
Safety and Health
As safety and health risk management, we are implementing potential risk management by "compliance with laws and regulations," and industrial safety risk management for potential risks that are "matters exceeding laws and regulations."
Concerning compliance with laws and regulations, we carefully inspect the action status for legal requirements that have been organized for each plant, laboratory, office, and other bases. In addition, the departments involved in EHS promotion conduct risk analyses at each site and promptly visit sites with particularly concerning risks to perform internal audits (EHS Self-Inspection). At sites with lower risk concerns, the departments described above conduct internal audits at least once every three years. Through internal audits, we assess the appropriateness of operations based on laws and regulations and check for any omissions. Any deficiencies are corrected to ensure continuous improvement towards full compliance with laws and regulations related to occupational health and safety.
Matters exceeding laws and regulations, such as the fact that the pharmaceuticals we manufacture are not subject to occupational exposure limits set by the government, pose potential risks. For example, employees handling these pharmaceuticals may be exposed to quantities that exceed the levels at which the pharmaceuticals exert their effects. Concerning the aforementioned risks where employees are exposed to chemical substances handled at plants and laboratories, we implement risk assessment and exposure measurement and take appropriate measures based on the risk. In addition, concerning potential risks in daily operations and risks leading to accidents, we implement risk assessment to identify issues. For risks at the middle level or higher, we are working to improve them. These activities are shared and opinions on them are exchanged at the safety and health committee at each site and at the EHS committee that is held semi-annually. We thereby strive to provide a safe work environment for employees. In addition, at the safety and health committee, the correction of issues identified during safety and health patrols, which are implemented from the perspectives of checking fire prevention measures and disaster-prevention equipment, such as fire, etc., checking the safe handling of machines, checking the completeness of safety operations, checking transfer operations, checking sorting, organizing, and cleaning, etc., are discussed.
At offices in headquarters where a health committee is established, various measures to maintain employee health are examined at monthly health committees based on the results of work environment measurements. In addition, a central health committee is held semi-annually to share information and exchange opinions concerning reporting on health management activity status, company-wide health matters, and details and issues examined at safety and health committees at each site.
In FY2023, the number of lost time injuries (not less than 1 day off) was 0 and lost-time injuries frequency rate was 0. For details including past data, please click here.
Emergency Management
To respond to any emergency situation, such as large earthquakes, natural disasters caused by climate change and fire, etc., we have established disaster prevention plans and hold regular training in line with the “crisis response/business continuity manual” to secure people’s lives and minimize asset losses.
Employee education and training
To promote EHS, each employee should understand its meaning correctly and be aware of their role and responsibility in promoting EHS. We educate our employees regularly (legal interpretation, EHS management system, work-related accident examples, control of chemicals, etc.). In FY2023, we held four participatory seminars (safety datasheet reading, risk assessment methods, etc.), attracting a total of 501 highly motivated employees (15%).